Iron Smelt Vinderheima Apr 2008
Date: 13 April, 2008
Location: Vinderheima
Premise:
- Test the "DARC Dirt 1" ore analog.
- Test the new sliding air flow control.
Experiment Notes - Econo-Norse Smelter in a can
Diameter: |
20 cm |
Stack above Tuyure: |
40 cm |
Tuyure Diameter: |
1" (2.6 cm) I.D. |
Tuyure Distance above floor: |
25 cm |
Tuyure Angle: |
20° |
Tuyure Penetration into stack (start/finish) |
3 cm / N/A |
The Team:
Leader |
Darrell Markewitz |
Staff |
Ken Cook |
Recorder |
Neil Peterson |
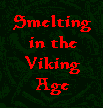 |
Reports of all of our iron smelting efforts along with more articles and information are available on the "Iron Smelting in the Viking Age" CD from the Wareham Forge. Copies of the CD can be purchased here. |
Smelt Totals
Total Charcoal |
30 Kg |
Weight of Bloom |
2 Kg |
Total Elapsed Time: |
4:30 |
Total Ore |
18 Kg (15.8 Kg dry) |
Weight of Slag: |
|
Bloom Quality |
|
Discussion:
The idea was to build a more durable version of the dependable Econo Norse firebrick smelter. The drum was just about exactly the same size as a hexagon arrangement of standard hard bricks - stacked the normal three sets tall. The result is a smelter containment that is roughly 20 cm internal diameter, but still at the normal plus 40 cm above the tuyere. The smaller diameter means that 2 buckets of charcoal (4 Kg) will fill the smelter rather than the usual 4 buckets (8 Kg). This means we want to target a slower burn rate (16 min / bucket) to maintain the contact time for the ore.
This smelt was to be a second test of the DARC Dirt 1 - bog iron ore analog developed by Gus Gissing. The first test (at Smeltfest 08) was not ideal, as the smelter layout was a new type we had little experience with. The dynamics of the 'bellows plate' type furnace, and its taller stack height combined to a low yield and very high carbon bloom. In this case the mix of 80% 'Spanish Red' (Fe2O3) / 10% silica sand / 10% flour had been air drying for about a week. The cold and wet weather had slowed this process. At the time of the smelt the ore material was dry enough to easily handle, but still slightly damp to the touch. It was broken up from the large plate pieces (roughly 1 cm thick) by tapping through a 2.5 cm wire grid with a wooden mallet. A second screen, about 3 mm, was used to separate out the fine dust. (This step was not done for the Smeltfest test). The result was pulling off about 20 % of the prepared material as dust. As the analog was not baked this time, this dust can easily be incorporated into the next batch by just adding water. It was generally thought that the pieces from the 2.5 cm grid may have been a bit too large. Use of a 1.5 cm grid is likely ideal.
The extraction was from the bottom of the furnace, which had been constructed with a proportionally large tab arch. As it turned out, there was a reasonably large slag block formed. The bloom proved properly positioned, and contained within the correct pool of liquid slag. With a bit of hammering, it was possible to break away the side of the slag and grab out the bloom.
The bloom was both smaller and less dense than I had hoped for. The yield is a bit better than it looks at first glance. We baked dry a measured sample of the ore analog, and it was found to contain 12 % water. This puts the 'real' weight of ore used at closer to 15.8 kg. This gives us a yield of about 13%. Still lower than our usual, but enough that the DARC Dirt 1 analog is worthy of further testing. There is still a very large mass of hardened slag to break free of the interior of the furnace. This may prove to have other smaller masses of metal contained in it. Certainly it would appear that there is a larger proportion of slag formed than has been seen in past uses of the larger brick furnaces with other ore types.
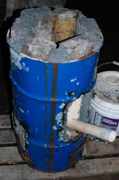 |
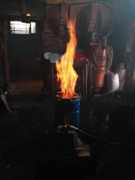 |
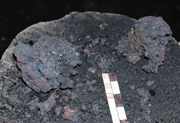 |
|
Overview of the smelter |
Smelter in action |
Finished (compacted) bloom pieces |
CLOCK |
ELAPSED |
EVENT |
AIR |
|
|
CHARCOAL |
|
|
ORE |
|
|
|
|
|
|
|
UNIT |
COUNT |
TOTAL |
COUNT |
TOTAL |
|
|
|
gage |
LpM |
P |
bucket |
|
kg |
|
kg |
|
|
|
|
|
|
|
|
2 |
|
|
12:00 |
|
start wood splints pre-heat |
|
|
|
|
|
|
|
|
12:45 |
:45 |
gentle air |
|
|
|
|
|
|
|
|
13:15 |
|
burn to natural base @ - 15 cm |
|
|
|
|
|
|
|
|
13:17 |
1:17 |
1st addition rough charcoal |
4 |
|
2 |
1 |
|
|
|
|
13:23 |
|
fill to tuyere, ensure still lit |
|
|
|
|
|
|
|
|
13:25 |
1:25 |
fill with rough charcoal |
|
|
|
|
|
|
|
|
|
|
|
|
|
|
|
|
|
|
|
12:00 |
|
start main smelt sequence |
54 |
* 450 |
|
|
|
|
|
|
12:10 |
0:10 |
start adding first charocal |
|
|
|
|
|
|
|
|
12:20 |
0:10 |
rough charcoal |
|
|
|
1 |
1 |
2 |
|
|
12:35 |
0:15 |
rough charcoal |
|
|
|
1 |
2 |
4 |
|
|
12:49 |
0:14 |
switch to graged fuel |
|
|
|
1 |
3 |
6 |
|
|
13:05 |
0:16 |
|
|
|
|
1 |
4 |
8 |
|
|
13:20 |
|
adjust air (reduce) |
49 |
400 |
6 |
|
|
|
|
|
13:21 |
0:16 |
|
|
|
|
1 |
5 |
10 |
|
|
13:32 |
0:11 |
|
|
|
|
1 |
6 |
12 |
|
|
13:39 |
|
start first ore addition |
|
|
|
|
|
|
|
|
13:45 |
0:16 |
|
|
|
|
1 |
7 |
14 |
1 |
1 |
13:55 |
0:10 |
|
|
|
|
1 |
8 |
16 |
1 |
2 |
13:59 |
|
air reduced |
|
365 |
|
|
|
|
|
|
14:11 |
0:12 |
|
|
|
|
1 |
9 |
18 |
2 |
4 |
14:27 |
0:16 |
|
|
|
|
1 |
10 |
20 |
2 |
6 |
14:41 |
0:14 |
|
|
|
|
1 |
11 |
22 |
2 |
8 |
14:58 |
0:17 |
|
|
|
|
1 |
12 |
24 |
2 |
10 |
15:12 |
0:14 |
|
|
|
|
1 |
13 |
26 |
2 |
12 |
15:26 |
0:14 |
|
|
|
|
1 |
14 |
28 |
2 |
14 |
15:43 |
0:17 |
|
|
|
|
1 |
15 |
30 |
2 |
16 |
16:00 |
0:17 |
|
|
|
|
1 |
16 |
32 |
2 |
18 |
16:14 |
0:14 |
start burn down |
|
|
|
1 |
17 |
34 |
|
|
|
|
|
|
|
|
|
|
|
|
|
16:35 |
|
extraction |
|
|
|
|
|
|
|
|
|
|
|
|
|
|
|
|
|
|
|
|
|
TOTALS |
|
|
|
|
|
|
|
|
|
|
|
|
|
|
|
|
|
|
|
|
|
Time |
4.5 |
hrs |
|
|
|
|
|
|
|
|
Ore |
18 |
kg |
|
|
|
|
|
|
|
|
Charcoal |
34 + |
kg |
|
|
|
|
|
|
|
|
|
|
|
|
|
|
|
|
|
|
|
Bloom |
2 |
kg |
|
|
|
|
|
|
|
|
Yield |
11 |
% |
|
|
|
|
|
|
|
|
|
|
|
|
|
|
|
|
|
|
|
Slag |
4.3 |
kg |
|
|
|
|
|
|
|
|
Gromps |
0.7 |
kg |
|
|
|
|
|
|
|
|
Total output recovered |
7 |
kg |
|
|
|
|
|
|
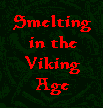 |
Reports of all of our iron smelting efforts along with more articles and information are available on the "Iron Smelting in the Viking Age" CD from the Wareham Forge. Copies of the CD can be purchased here. |